Induction melting furnaces and patili furnaces
Today, induction melting is widely used in the production and casting of steels, as well as the melting of aluminum, copper, zinc and other types of non-ferrous metals. Among the advantages of induction melting, for example, we can mention the high efficiency of materials and a clean environment, which has caused the desire of metal product manufacturers to induction melting furnaces.
In induction melting furnaces, the electric current induced by the magnetic field creates heat, and this heat melts the object (usually metals). ). The metal is placed in a bush around which magnetic coils are wrapped and.. The current in the magnetic coils causes heat and metal melting.
The most important induction furnaces are coreless induction furnaces and channel induction furnaces.
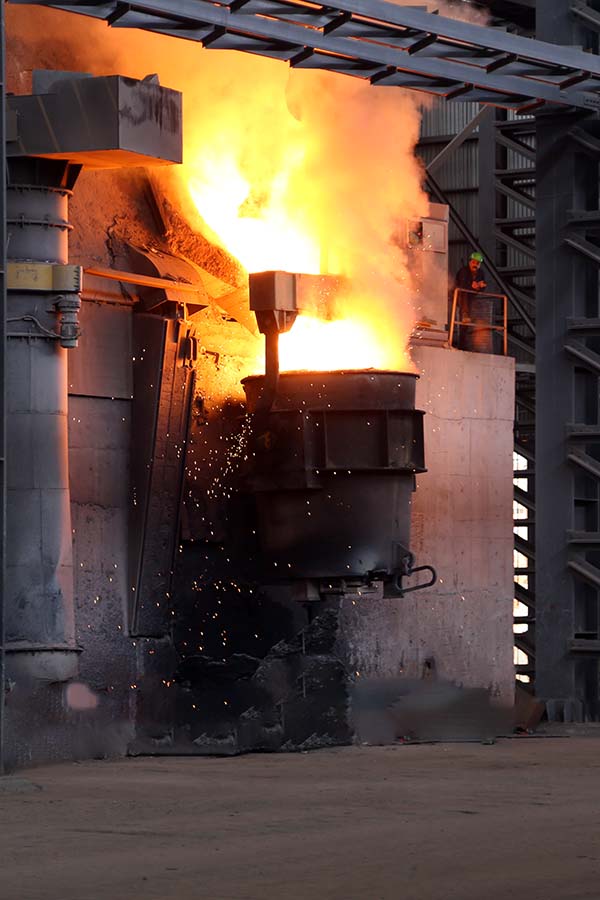
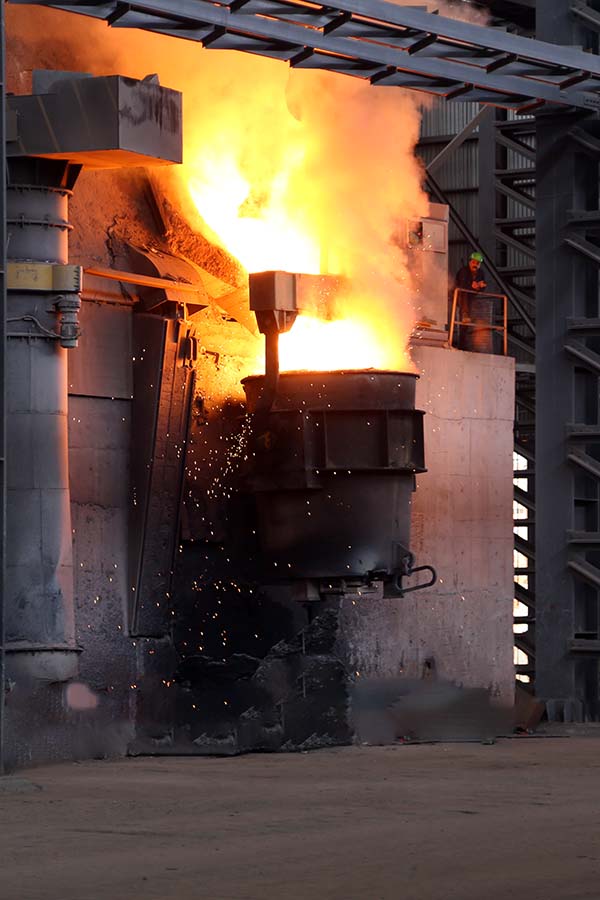
In a coreless induction furnace, the metal is kept inside a refractory casing surrounded by coils. In this case, the induction melting furnace is similar to a transformer in that the metal acts like a secondary coil in the transformer and by applying force to the primary coil surrounding the metal, eddy currents are induced and heat is generated. After the melting of the metal, stirring and homogenization happen naturally due to the presence of electromagnetic forces and currents. By carefully selecting the frequency and power, the speed of melting and homogenization can be controlled..
In the past, channel induction furnaces were generally used to keep molten metal at a certain temperature, but today they are sometimes used to melt metals as well. This . This furnace includes an inductor (progenitor) as a source of energy production, which consists of several coils that are cooled by water. These furnaces have less surface turbulence in the molten metal holding plant, as a result of which gas and volatile materials are difficult to escape. Therefore, for melting operation, coreless induction furnace is preferred and channel furnace is mostly used to keep the molten metal at a certain temperature..
The use of induction melting furnaces in capacities lower than 40 tons can lead to the production of melt with suitable and cheap quality. Among the advantages of this type of furnaces, we can mention easy operation and operation, as well as increasing the efficiency of metal melting. . The ability to start and start the furnace immediately reduces the time it takes to reach the working temperature. The existence of natural homogenization and production of clean melt and no need for high-cost pollution control systems are other advantages of induction furnaces.
Other positive points of these furnaces include the following:
- • High energy efficiency
- • Low cost of investment and peripheral equipment
- • Not needing a lot of space and the ability to increase the speed of melting in small furnaces
- • Significantly lower noise pollution compared to other types of melting furnaces
- • Less consumption of materials, especially non-refractory materials and reducing the time of replacing non-refractory coatings and no need to use graphite electrodes
On the other hand, the most important form of induction furnaces is the difficulty in the dephosphorization process and performing secondary metallurgical operations. Therefore, in addition to these furnaces, it is necessary to have crucible furnaces in order to perform the purification process and add alloy elements. . Another disadvantage of these furnaces is the lower production capacity compared to electric arc furnaces. . Also, in induction furnaces, scrap with the least pollution and oxide materials should be used, which is sometimes difficult and causes an increase in initial costs..
Also, the use of sponge iron as an auxiliary charge to adjust the chemical properties in these furnaces has improved the performance of induction melting furnaces. . Using sponge iron, the amount of molten carbon can be adjusted according to the desired specifications, and considering that there are no harmful elements and metals in sponge iron, the obtained molten metal will be clean and free of harmful elements..
Before entering the metal materials into the chemical analysis furnace, these materials are carefully controlled to achieve the final specifications of the product . If the amount of carbon, sulfur and phosphorus in the metal charge is high, the controlled amount of sponge iron is charged to the furnace, after completion 80% melting, a sample is taken from the furnace and if the amount of carbon is still high, the sponge iron is again charged to the furnace and by controlling other important elements in the steel structure such as silicon and manganese, the resulting melt is analyzed according to the standard and request.. on the other hand, it should be kept in mind that because sponge iron has porosity and this factor causes resistance to the passage of current, in order to avoid high electricity consumption, a maximum of 50-60% of the metal charge can be assigned to sponge iron gave New research and development in power supply with variable frequencies, improvement in refractory coatings, high power inductor design, furnace heat recovery and the use of computer and automation systems have improved the efficiency of induction melting furnaces and the tendency to These types of furnaces have been used more. In addition, in recent years, with the technology of twin induction furnaces that have two furnaces, it has been possible to increase the efficiency and speed of melt production..
After the initial preparation of the melt in induction furnaces, for homogenization, analysis and to reach the temperature of the melt to the desired casting temperature, the resulting melt is transferred to the crucible furnace and after the completion of the above steps, it is transferred to the continuous casting unit.
The working principle of the electric arc furnace is exactly the same as the electric arc furnace, with the only difference being that instead of using the body of the electric arc furnace, the electric arc furnace itself is used as the body of the furnace in such a way that the electrodes embedded in the upper part of this equipment enter the electric arc furnace and with The creation of an electric arc is exactly the same as the welding electrodes, which performs the melting and temperature increase.
Due to the fact that there is no Foucault currents in crucible furnaces to create melt vortex for homogenization, neutral gas injection such as argon or nitrogen is used to stir the melt and through injection from the bottom of the crucible into the melt.
In the past, channel induction furnaces were generally used to keep molten metal at a certain temperature, but today they are sometimes used to melt metals as well. This furnace includes an inductor (progenitor) as a source of energy production, which consists of several coils that are cooled by water. These furnaces have less surface turbulence in the molten metal holding plant, as a result of which gas and volatile materials are difficult to escape. Therefore, for melting operation, coreless induction furnace is preferred and channel furnace is mostly used to keep the molten metal at a certain temperature..
The use of induction melting furnaces in capacities lower than 40 tons can lead to the production of melt with suitable and cheap quality. . Among the advantages of this type of furnaces, we can mention easy operation and operation, as well as increasing the efficiency of metal melting. The ability to start and start the furnace immediately reduces the time it takes to reach the working temperature. The existence of natural homogenization and production of clean melt and no need for high-cost pollution control systems are other advantages of induction furnaces.
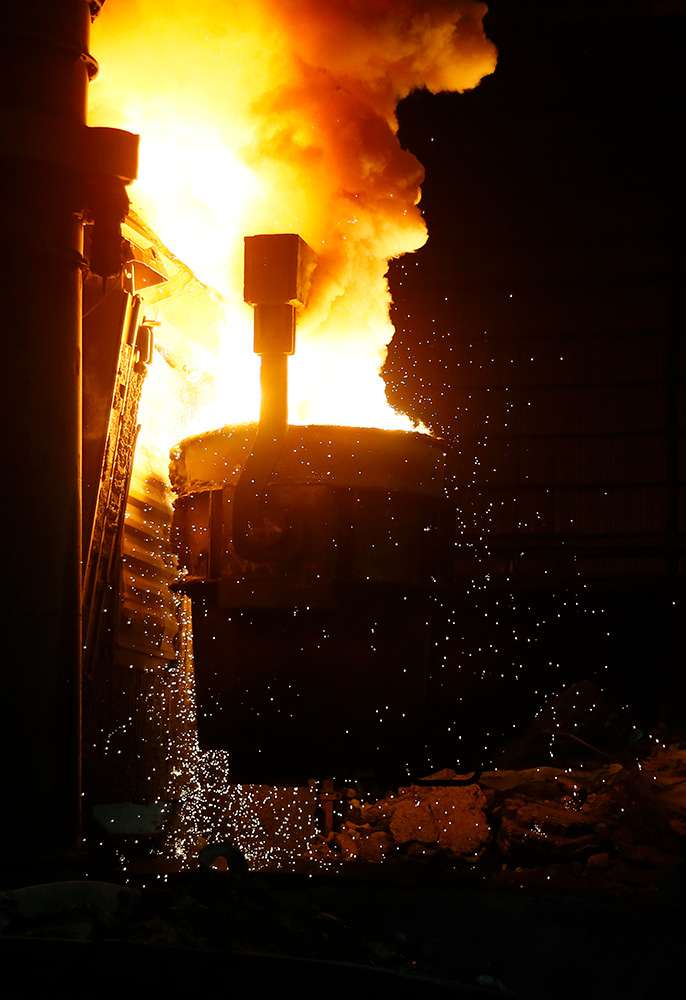
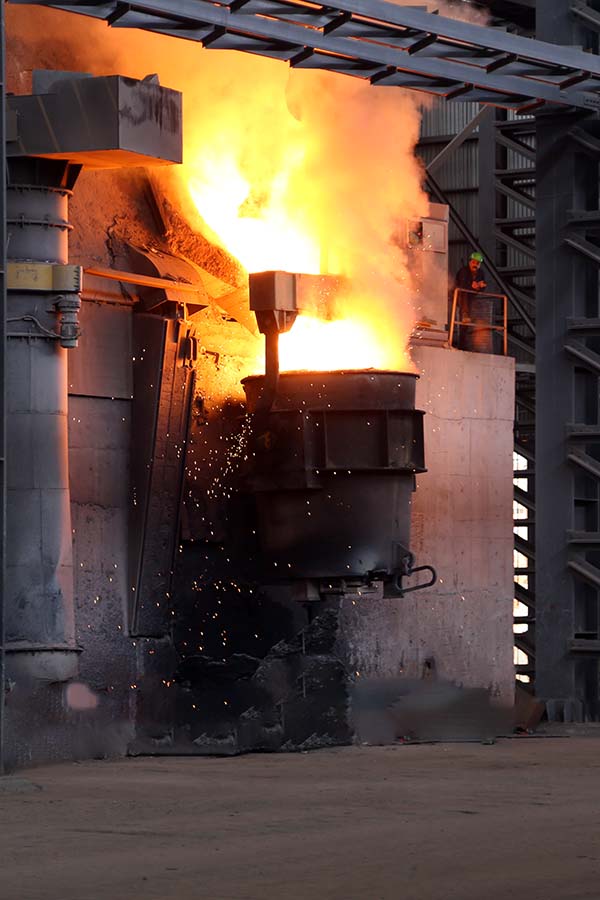