Smelting and casting factory
The smelting and casting factory is one of the three production units of Bisotoun Steel Complex, whose task is to produce steel ingots in grades 5SP, 3SP and ST52.
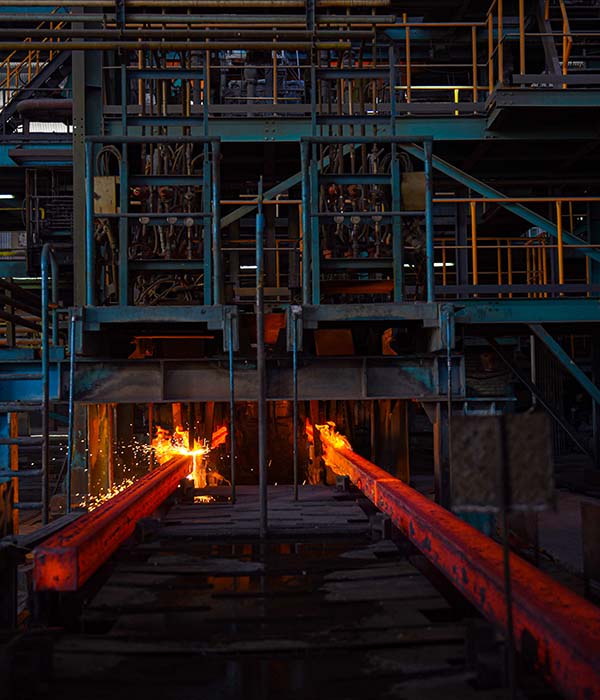
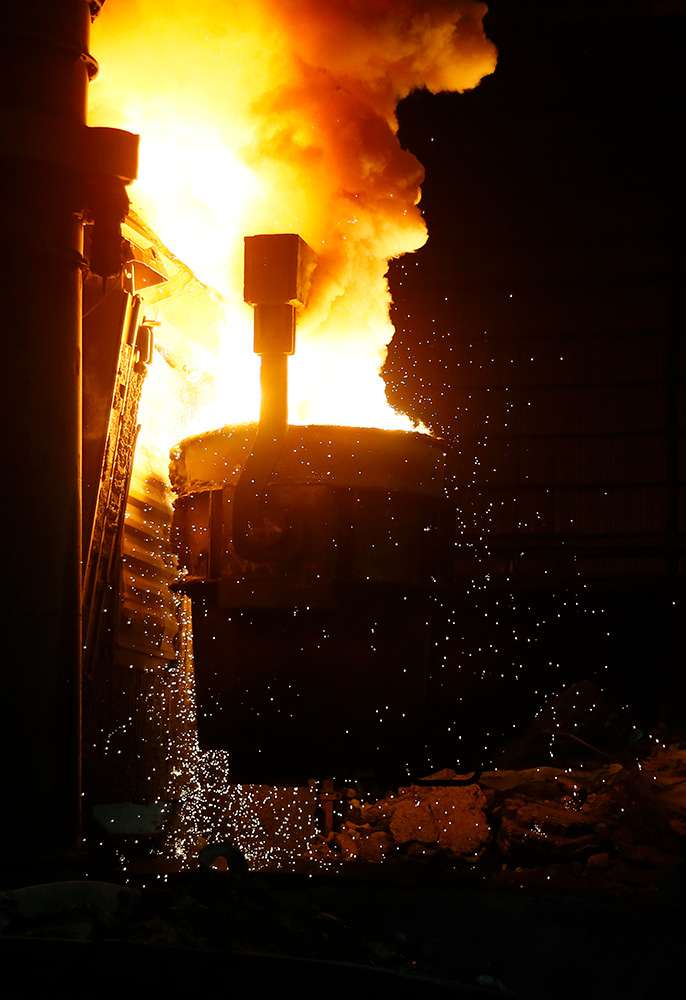
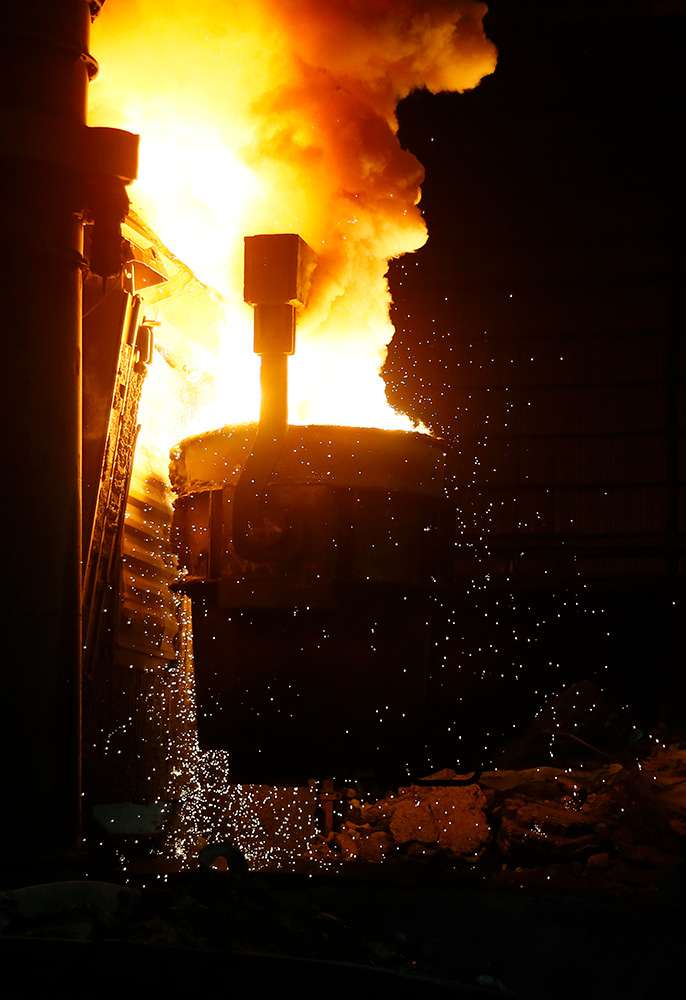
Introduction of melting and casting unit
In order to get to know more about this factory, its units are briefly described in the following order.
1: 1: Waste processing unit and supply of sponge iron
In this unit, the wastes brought to the factory are converted into pressed wastes, crushed wastes and ready to charge in induction furnaces. In this unit, in addition to the mentioned processes, separation and separation operations are also performed according to the type of wastes. . Also, the sponge iron produced in the reclamation unit is delivered to the smelting and casting unit along with the processed waste with the control and coordination of this part.
2: 2: Induction furnaces of melt production unit
The smelting and casting plant of Bisotoun steel complex, having 30 ton furnaces with 15 megawatt power, is responsible for the production of melt with a tonnage of 250,000 tons of steel ingots in all types of construction and alloy steels. . In the melt production unit, 4 induction furnace plants with a capacity of 30 tons, which can produce up to 35 tons of melt, are used and have the ability to produce 60 tons of melt per hour.
Patili refining furnace LRF
The mechanized Patili refining furnace, similar to the electric arc furnace, completes the operations of analysis, homogenization, quenching, desulfurization of the melt created in induction furnaces. The advantage of using the Patili furnace is that it provides the ability to prepare all kinds of alloy steels, and due to its phosphorus and sulfur removal properties, it provides the possibility of using iron ore in the production process of sponge iron.
4: 4: Quality control unit and metallurgy laboratory
In this unit, the molten sample taken from the production unit is analyzed by a mass spectrometer or quantometer, and the percentage of elements necessary to reach the standard steel analysis is determined. And the smelting production unit is informed and the permitted additives, which include ferro-silico-manganese, ferro-silica and ferro-manganese, are determined and added to the smelting.
5: 5: Overhead cranes for transporting melt and materials
The smelting and casting factory, having overhead cranes with different tonnages from 10 tons to 100 tons, are in charge of transporting and moving raw materials and produced melt.
6: 6: Molten carrying bottles
In order to move the melt produced in the induction furnaces and transfer them to the casting unit, 6 35 ton melting machines are transported by 100 ton cranes to transport the melt from the Patil preheat station to the bottom of the induction furnaces and after pouring the melt from inside The furnace is transferred to the melting crucibles to the casting station.
7: 7: CCM casting station and continuous casting machine
The continuous casting machine of the smelting and casting plant of the Bisotoun Steel complex includes 2 strands of the casting line, which turns the melt produced in the melting unit into steel ingots at a speed of up to 4 times per minute. Therefore, the production process in the casting station is as follows. The standard melting pot is placed by 100 ton melting cranes on the work ladle or the pot carrying machine, and the work ladle transfers the pot to the center of the tundish, which is the interface between the tundish and the casting mold, after adjusting the position of the tundish relative to the tundish. The slide gate system or the hydraulic sliding valve under the pot is opened and the melt is transferred from the pot to the tank. . According to the number of casting lines, there are melt exit nozzles under the tundish, which direct the melt from inside the tundish into the casting molds. Casting molds that are placed on the oscillator tables are oscillated by the oscillator device and the melt directed to the die turns the mold into ingots and is gradually cooled in the cooling chamber until it reaches the ingot bed and transfer. It can be loaded into the product warehouse
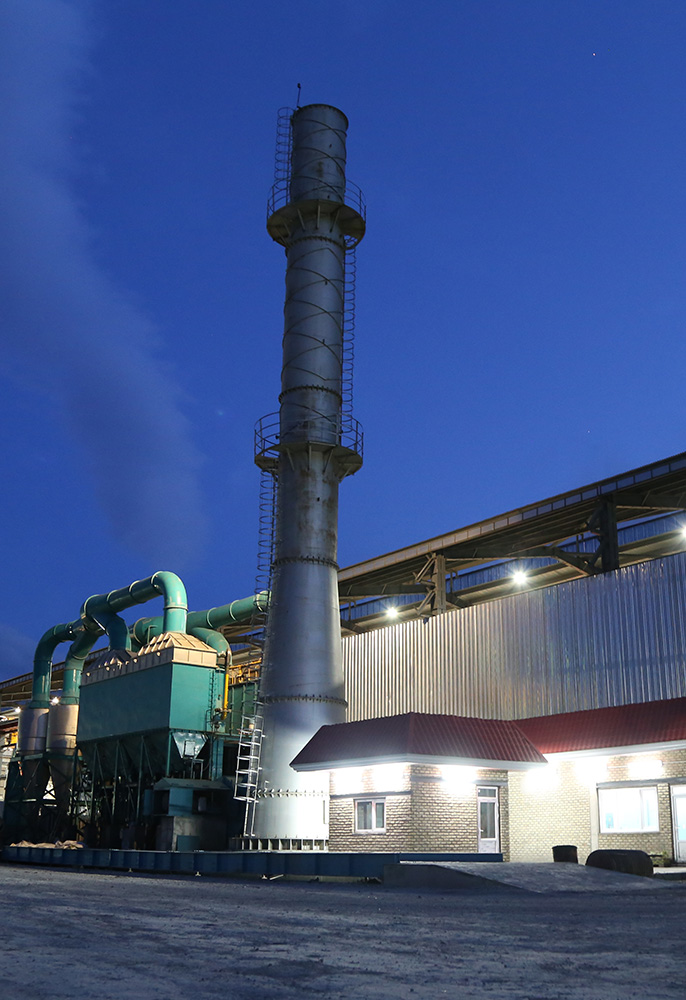
The product produced in the smelting and casting factory
The production product of this unit is steel ingot with a cross-section of 150*150 square centimeters, which, as mentioned earlier, is obtained by continuous casting method. Due to the presence of the Patil Refining Furnace (LRF) unit, this company is able to produce all kinds of alloy steels, including 5SP, 3SP and ST52 grades for construction and industrial use. It should be noted that the presence of the quality control unit and the experienced laboratory of this factory in the entire production process has led to the addition of permitted additives, including ferrosilico-manganese, ferrosilicon and ferromanganese, to the melt with high precision and calculations, and this has led to the production of The steel is in accordance with international standards.
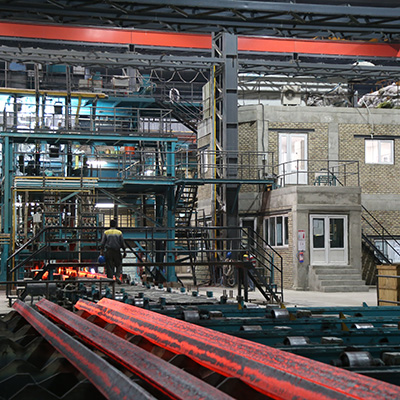
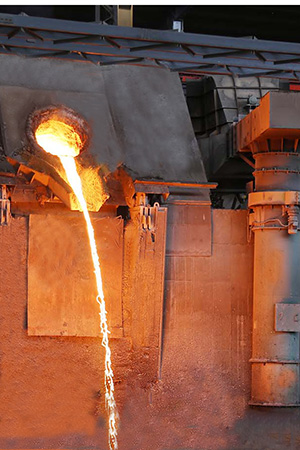
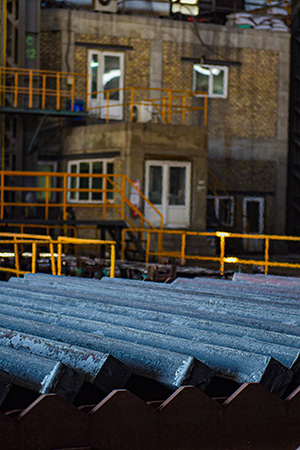
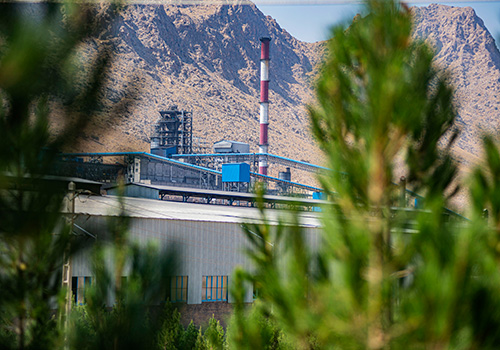
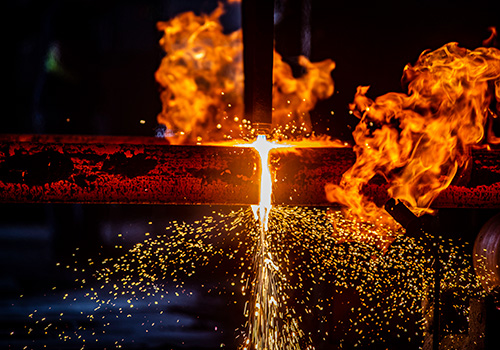
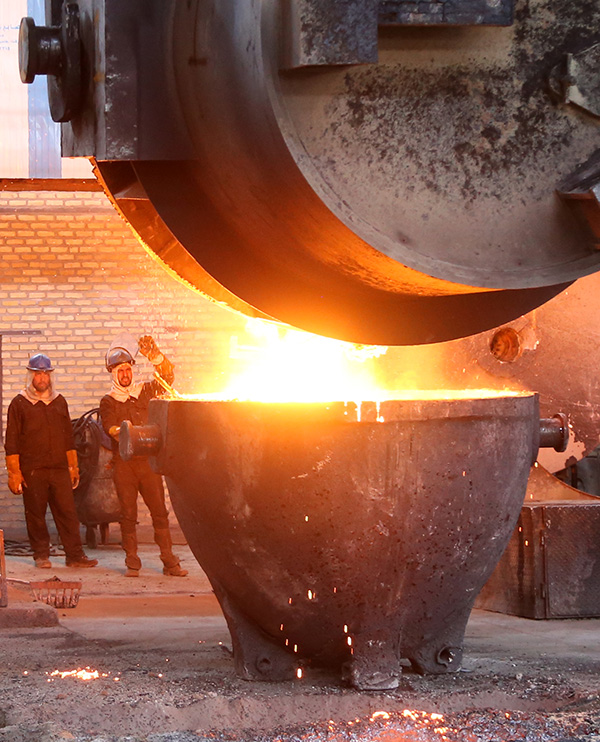
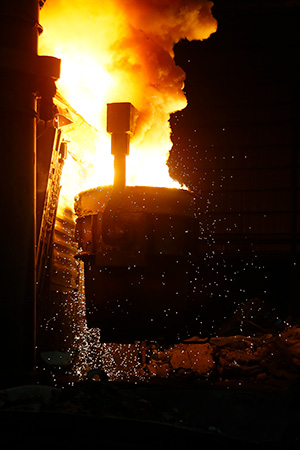
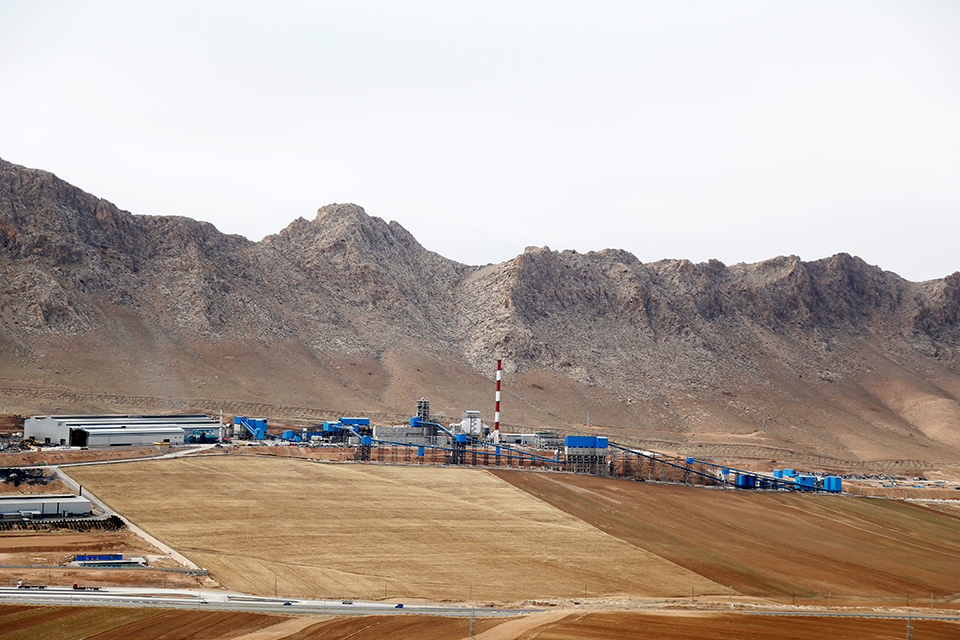
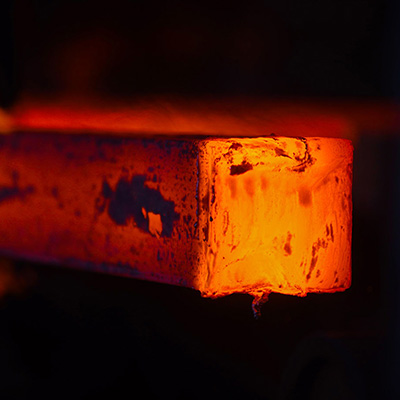
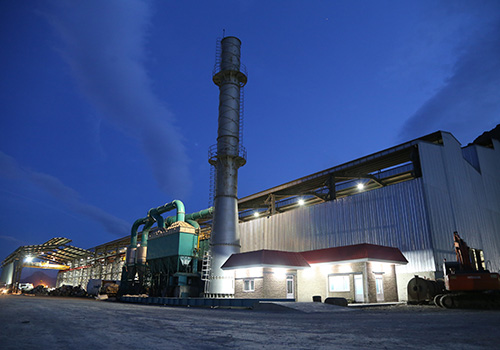